Magnesium die casting is a manufacturing process that involves the use of magnesium alloys to create complex shapes and components. The process is widely used in the automotive, aerospace, and electronics industries, where lightweight, strong, and durable components are required. In this blog post, we will explore what magnesium die casting is, how it works, and its advantages and disadvantages.
What is Magnesium Die Casting?
Magnesium die casting is a process that involves injecting molten magnesium alloy into a steel mold under high pressure. The mold is designed to create the desired shape of the component. Once the molten metal is injected into the mold, it cools and solidifies, forming the final product. The process is repeatable, which means that multiple identical components can be produced quickly and efficiently.
Magnesium alloys are made up of magnesium, aluminum, and zinc, and are known for their excellent strength-to-weight ratio. They are also highly resistant to corrosion, making them ideal for use in harsh environments. Magnesium alloys are lightweight, which reduces the weight of the final product, resulting in improved fuel efficiency in the automotive industry and reduced material costs in other industries.
How Does Magnesium Die Casting Work?
The magnesium die casting process involves several steps. First, the mold is designed and manufactured to the desired shape of the component. The mold is made of steel and can be reused multiple times. Next, the magnesium alloy is melted in a furnace and injected into the mold under high pressure. The pressure ensures that the molten metal fills the entire mold and creates the desired shape.
After the molten metal cools and solidifies, the mold is opened, and the finished component is removed. The component may require additional finishing, such as trimming, deburring, and polishing, to achieve the desired surface finish. The finished component is then inspected for quality and sent for further assembly or packaging.
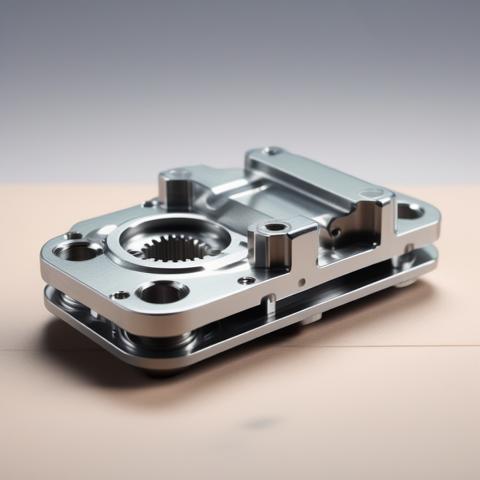
Magnesium die casting
Advantages of Magnesium Die Casting
Magnesium die casting offers several advantages over other manufacturing processes. First, it allows for the creation of complex shapes and thin-walled components that would be difficult or impossible to produce using other methods. Second, it is a highly repeatable process, which means that multiple identical components can be produced quickly and efficiently. Third, magnesium alloys are lightweight and strong, which reduces the weight of the final product and improves fuel efficiency in the automotive industry.
Disadvantages of Magnesium Die Casting
Despite its many advantages, magnesium die casting has some disadvantages. First, magnesium alloys are more expensive than other metals, such as aluminum and steel, which can increase the cost of the final product. Second, magnesium alloys are highly reactive and can be difficult to handle, which requires specialized equipment and training. Third, magnesium alloys are highly flammable and can ignite when exposed to heat or sparks, which requires careful handling and storage.
Conclusion
Magnesium die casting is a highly versatile manufacturing process that offers several advantages over other methods. It allows for the creation of complex shapes and thin-walled components, is highly repeatable, and produces lightweight and strong components. However, it also has some disadvantages, including the high cost of magnesium alloys, the difficulty of handling and storing them, and their flammability. Overall, magnesium die casting is a valuable process that can help manufacturers create high-quality components efficiently and cost-effectively.
Aluminum gravity casting is a popular manufacturing process utilized in the production of a wide range of products. This process involves pouring molten aluminum into a permanent mold under the force of gravity. The mold is typically made of steel or iron and is designed to produce complex shapes with high precision. This process is ideal for producing large quantities of parts with consistent quality, making it a cost-effective solution for many industries.
The process of aluminum gravity casting offers several advantages, including the ability to produce parts with excellent surface finishes, high strength-to-weight ratios, and good dimensional accuracy. Additionally, this process is highly versatile and can be used to produce a wide range of products, from automotive parts to consumer goods. Overall, aluminum gravity casting is a reliable and efficient manufacturing process that is widely used throughout the industry.
Welcome to GC Precision Mould, your premier China die casting manufacturer and China Mold Maker. We specialize in producing high-quality plastic molds, die casting molds, and a wide range of die cast parts from materials such as aluminum, zinc, and magnesium.
At GC Precision Mould, we are dedicated to providing our clients with the best possible aluminum die casting and other casting products and services. Our team of experienced engineers and technicians use the latest technology and techniques to ensure that every part we produce meets the highest standards of quality and accuracy.
GC mold offers semi solid aluminum die casting and 6063 pure aluminum die casting products as well, if you want to know more about semi solid casting, please go to semi solid aluminum die casting page to know more.
Our products are widely used in a variety of industries, including automotive, consumer electronics, medical, and industrial equipment. We work closely with our clients to understand their specific needs and develop custom solutions that meet their unique requirements.
Whether you need a single plastic mold or a complete die casting production line, we have the expertise and resources to deliver exceptional results. Contact us today to learn more about our services and how we can help you achieve your manufacturing goals.
If you have a project that needs Die casting China for your die casting project or mould suppliers to make injection molding products, contact us to get the best price now.
Recent Comments